What Are Molybdenum Glass Melting Electrodes?
Molybdenum electrodes are solid rods or plates that sink into the molten glass bath of electric melting furnaces. Their job is simple: channel high current into the glass, so it heats evenly and stays molten. You’ll find them in all shapes and sizes—straight bars, tapered pins, even custom cross‑sections—always made from high‑purity molybdenum to handle extreme heat, corrosion, and wear.
These aren’t luxury parts. They’re workhorses. Molybdenum barely bats an eye at 1,400–1,600 °C. While copper or steel would warp or dissolve, molybdenum holds its ground. That rough‑and‑tumble toughness is why it’s the first pick for serious glass melting.
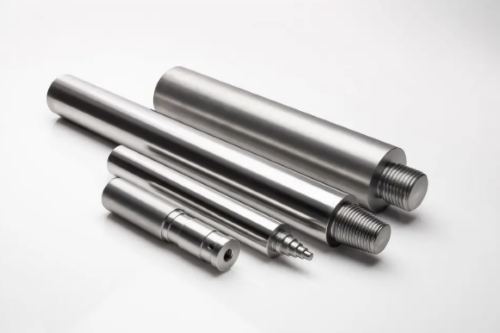
Why Do We Use Molybdenum Glass Melting Electrodes?
Glass needs consistent heat to flow right. If the temperature swings or drops, you end up with unmelted bits, bubbles, or unwanted color shifts. Molybdenum solves that by:
- High‐temperature strength
It keeps its shape well above 1,400 °C, so electrodes stay straight and predictable.
- Good conductivity with low self‑heating
You want current in the glass, not wasted heating the electrode itself. Molybdenum strikes a solid balance.
- Built‑in corrosion guard
In an oxidizing furnace, molybdenum makes a thin oxide film that slows further attack. Other metals just vanish.
In practical terms, that means fewer electrode swaps, more batches per campaign, and a cleaner end product. You don’t stop production every few days to replace parts, and you get steady quality from the first melt to the last.
Further reading: Molybdenum Electrodes for Glass Furnaces
Where to Use Molybdenum Glass Melting Electrodes
When I say “where,” I mean the exact corners of the glass world where molybdenum electrodes do their best work:
- Display‐panel glass
In factories producing LCD or OLED screens, they use large tank furnaces with top electrodes to melt the ribbon of ultra‑pure soda‑lime or aluminosilicate glass. Molybdenum rods, set in precise arrays, help keep the ribbon thickness uniform and free of striations.
- Fiber‑optics preforms
Here, the glass is often quartz or fluorophosphate, melted in small crucibles. A single molybdenum pin stirs or maintains temperature in that tiny, specialty melt, so the fiber draw is smooth and defect‑free.
- Laboratory and pharmaceutical glass
When you need borosilicate or specialty labware, small all‑electric furnaces use side‑entry electrodes. Molybdenum plates deliver heat evenly, making sure test tubes, pipettes, and specialty vials come out with no stress cracks.
- Solar‐panel glass
Producing ultra‑clear, low‑iron glass for photovoltaic modules calls for hybrid furnaces—part electric, part gas. Molybdenum electrodes support the electric side, giving tight control over temperature gradients so the final sheets have no internal flaws.
- Colored and art glass studios
Even small‑batch studios that supply decorative or stained glass lean on mini‑electrodes in tabletop furnaces. That precise heat helps artists layer colors and textures without devitrification or fracturing.
- Industrial and chemical glass
Fused silica for chemical reactors, glass liners for vessels, and glass‑to‑metal seals all get an assist from molybdenum heating elements in their melting stages. Consistent temperature means predictable viscosity and fewer rejects.
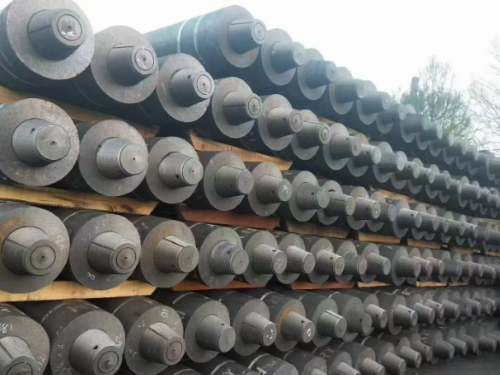
How to Use Molybdenum Glass Melting Electrodes
Installing these electrodes is straightforward but calls for care:
- Positioning
Electrodes sit horizontally or vertically, depending on furnace style. You want the electric arc or conduction path right where the glass is thickest, so no cold spots or overheated corners.
- Water‐cooled supports
The clamped ends live in holders with water jackets. Even though molybdenum can take the heat, those clamps and feedthroughs can’t. Cool ’em down so you avoid warping or stress at the hot junction.
- Gentle handling
At room temperature, molybdenum is a bit brittle—like ceramic. You won’t shatter it by tossing it around, but avoid sharp knocks or over‑tightening clamps.
- Regular inspection
A quick visual check before each run spots pitting or uneven wear. Replace or re‑machine electrodes before they get too thin or develop deep grooves.
Get these steps right, and the electrodes stay in service for months instead of weeks. Less downtime, fewer surprises, and a smoother production run.
Other Molybdenum‑Based Materials Used in the Glass Industry
Molybdenum’s talents aren’t limited to electrodes. You’ll also see it in:
- Crucibles for specialty melts
High‑purity quartz or phosphate glass melts in molybdenum crucibles to keep impurities out. Perfect for fiber‑optics preforms or specialty display glass.
- Linings and shields
Sheets or tiles of molybdenum line furnace walls around the hot zone, protecting steel shells from aggressive slags and radiant heat.
- Stirring and homogenizing rods
In processes that need mixing—like batch blending of colorants—molybdenum rods serve as long‑lasting stirrers, resisting attack by molten frit.
- Alloyed components
Add lanthanum or zirconium to molybdenum for parts that need extra toughness or a bit more oxidation resistance. You’ll find these in electrode holders, stirrer shafts, and thermocouple sheaths.
- Mesh screens and filters
Molybdenum wire meshes filter out unmelted chunks or contaminants as glass pours from the furnace into forehearths.
- Thermocouple and sensor protection
Sheaths made of molybdenum guard delicate sensors inside the melt, so you get accurate temperature readings without the sensor dissolving.
Conclusion
In short, molybdenum is exactly what a seasoned glass‑melting operation needs. Whether you’re crafting the next generation of flat panels or pulling kilometers of optical fiber, Mo electrodes and their cousins keep the heat steady and the glass pure. That’s why, in the right fields and detailed applications, molybdenum remains the quiet hero behind the furnace door. For more information, please check Advanced Refractory Metals (ARM).
REVIEWS
{{viewsNumber}}
Thought On "{{blogTitle}}"
LEVE A REPLY(Cancle reply)
Your email address will not be published. Required fields are marked*
{{item.children[0].name}}
{{item.children[0].created_at}}
{{item.children[0].content}}
More Replies
LEAVE A REPLY
Your email address will not be published. Required fields are marked*