Introduction
Measuring the hardness of materials is a fundamental process in materials science, metallurgy, and engineering. It provides critical insights into their durability, resistance to wear and deformation, and suitability for specific applications.
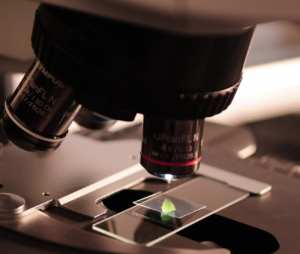
There are several methods for measuring hardness. Each of them is suited to different materials and hardness ranges. This article explores five principal ways to measure material hardness: the Vickers, Brinell, Rockwell, Mohs, and Knoop tests. Hope that you can learn about their unique features and applications.
Understanding Material Hardness
Material hardness refers to a material's resistance to permanent deformation, typically by penetration, indentation, or scratching. This property varies widely among different materials, influencing their application and suitability for specific uses. Below, we explore the common hardness of various materials, from metals and polymers to ceramics and composites.
--Metals
- Aluminum: Al has a relatively low hardness, typically around 60-70 on the Brinell hardness scale.
- Titanium: This strong, corrosion-resistant metal has a Brinell hardness range of 300-400. It is harder than many steels but still workable.
- Tungsten Carbide: Not a pure metal but a metal matrix composite, tungsten carbide is extremely hard. It comes with values exceeding 1500 on the Vickers hardness scale.
--Polymers
- Polyethylene (PE): Soft and flexible, PE comes with a Shore hardness ranging from 40D to 70D for high-density variants.
- Polyvinyl Chloride (PVC): Its hardness ranges from soft (Shore A 70-100) when plasticized to rigid (Shore D 80+) in its unplasticized form, used in pipes and fittings.
--Ceramics
- Alumina (Aluminum Oxide, Al2O3): This common ceramic material used in abrasives and cutting tools possesses a Vickers hardness of approximately 1800-2200.
- Silicon Carbide (SiC): Extremely hard and thermally conductive, silicon carbide is used in high-performance brake disks and semiconductor devices because it has a hardness of around 2500 on the Vickers scale.
- Zirconia (ZrO2): Known for its toughness and resistance to crack propagation, zirconia has a Vickers hardness of about 1200-1500.
--Composites
- Carbon Fiber Reinforced Plastics (CFRP): While the hardness of composites can vary widely, CFRPs offer high strength-to-weight ratios and have hardness values that can be tailored through the matrix and fiber properties.
- Ceramic Matrix Composites (CMCs): Incorporating ceramic fibers into a ceramic matrix, CMCs are designed for high-temperature applications. Its hardness values exceed those of most metals and polymers.
1. Vickers Hardness Test
The Vickers hardness test derives from the early 20th century. It is notable for its wide application range, from soft metals to the hardest.
- It involves pressing a diamond pyramid indenter with a square base and an angle of 136° between opposite faces into the material under a specific load.
- The load varies depending on the material being tested but is typically applied for 10-15 seconds.
- The hardness value is calculated from the diagonal length of the indentation left by the indenter, with no need to change the indenter for different hardness scales.
It has become a versatile choice for measuring the hardness of materials across a broad spectrum.
2. Brinell Hardness Test
The Brinell hardness test is one of the oldest and most commonly used methods. It is especially suitable for materials with coarse or uneven grain structures, such as cast iron, steel, and non-ferrous metals.
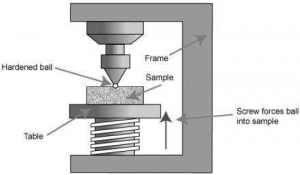
Brinell Hardness Test Devices [1]
- It involves pressing a hard steel or carbide ball of a specified diameter (usually 10 mm) into the material under a fixed load (commonly 3000 kg for steel) for a set period.
- The hardness number is derived from the load divided by the surface area of the indentation.
- The Brinell test is favored for its simplicity and the large indentation it produces, which averages out heterogeneities in the material.
3. Rockwell Hardness Test
The Rockwell hardness test is one of the most frequently used methods due to its quick execution and direct readout capabilities.
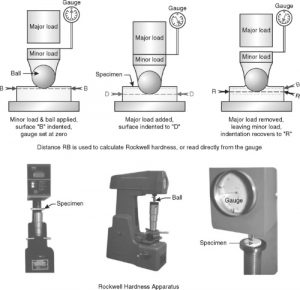
Rockwell Hardness Test [2]
- It measures the depth of penetration of an indenter under a large load (major load) compared to the depth under a preliminary minor load.
- The indenter can be either a diamond cone or a hard steel ball, depending on the material being tested.
- The Rockwell scale is divided into different scales, denoted by letters (e.g., HRC for hard materials, HRB for softer materials).
- It is versatile for a wide range of materials. Its non-destructive nature and rapid results make it ideal for quality control processes.
4. Mohs Hardness Test
The Mohs hardness test was created in the 19th century by Friedrich Mohs.
- It is a qualitative method used primarily for minerals.
- It ranks materials on a scale from 1 (talc) to 10 (diamond) based on the ability of a harder material to scratch a softer material.
- Although not precise enough for engineering applications, the Mohs test is simple to perform and useful for field identification of minerals and preliminary assessments of material properties.
5. Knoop Hardness Test
The Knoop hardness test, like the Vickers, uses a diamond indenter, but with an elongated pyramid shape.
- This test is particularly suited for brittle materials or thin sections, including ceramics, glass, and thin layers of coating, where minimal damage is essential.
- The Knoop indenter is pressed into the material under a light load, producing an indentation that is more elongated than that of the Vickers test.
- The hardness value is calculated from the longer diagonal of the indentation, allowing for precise measurements on micro-scales.
Conclusion
Each hardness testing method offers unique advantages and is suited to specific types of materials and applications. The choice of test depends on the material properties, the accuracy required, and the context of the testing (e.g., laboratory research, quality control, field testing).
Understanding the principles and applications of these tests is crucial for selecting the appropriate method to accurately measure the hardness of materials. In these ways, we can ensure their proper use and longevity in their respective applications.
Advanced Refractory Metals (ARM) stands as a premier manufacturer and supplier of Tungsten, Molybdenum, Tantalum, Rhenium, Titanium, Zirconium, and other advanced materials. ARM has been dedicated to delivering top-tier refractory metal products to a global clientele since its inception in 1994. For more information, please our homepage.
Reference:
[1] Gyurkó, Zoltán & Nemes, Rita. (2018). Energy-based evaluation of hardness testing with discrete element method. IOP Conference Series: Materials Science and Engineering. 426. 012013. 10.1088/1757-899X/426/1/012013.
[2] Campo, E. A. (2008). Selection of Polymeric Materials. William Andrew. https://www.sciencedirect.com/topics/chemistry/rockwell-hardness
REVIEWS
{{viewsNumber}}
Thought On "{{blogTitle}}"
LEVE A REPLY(Cancle reply)
Your email address will not be published. Required fields are marked*
{{item.children[0].name}}
{{item.children[0].created_at}}
{{item.children[0].content}}
More Replies
LEAVE A REPLY
Your email address will not be published. Required fields are marked*